Satisfaction
arises where good service exists
TCT - Always in good hands
Thanks to our experienced employees, we always keep a close eye on our customers’ needs. At TCT Induktionstechnik GmbH, creating and maintaining customer value is our highest priority. As a strong partner, we are at your side in all areas, from initial consulting and repair to on-site service. Among other things, we offer a wide range of services for induction systems from all leading manufacturers.
Repairs, service and maintenance
To ensure smooth and efficient production at your company, we are at your disposal with preventive service and maintenance work.
This includes, among consulting, on-site measurements, and testing services.
All repair work carried out is fully documented in detailed inspection report. Give us a call. Our experts are ready to assist you with advice and practical support.
We are experts in the repair / maintenance of:
- Complete coreless induction furnaces of all known brands
- Inductors for channel furnaces of all known brands
- Induction heating systems
- Coreless furnace coils of all known brands
- Furnace heads
- Channel furnaces of all well-known brands
- Inductors for forming processes
- Protective cylinders
- Power cable
- Magnetic yokes
Our test methods:
- Endoscopic examination
- Test field
- Insulation measurement
- Wall thickness measurement
- Thermal imaging
- Hot water test method
Retrofitting: Your partner from A to Z
We are your reliable partner for the support of your induction system or induction furnace over its entire life cycle. Production changes, technological advancements and different process conditions require constant further development of existing systems. Throughout the entire modernization process, we stand by your side as a strong partner and offer the following measures:
- Performance optimization and line upgrades of induction furnaces and systems
- Changes to furnace geometry and inductor
- Conversion of mechanical switchgear to IGBT converter technology
- Modification of power units
- Changes and modifications to components within the induction systems
- Control technology
- Modernization in the furnace head area
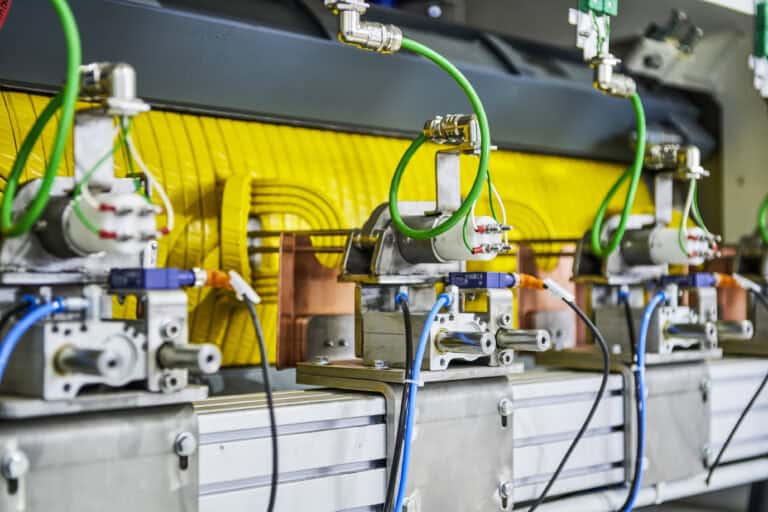
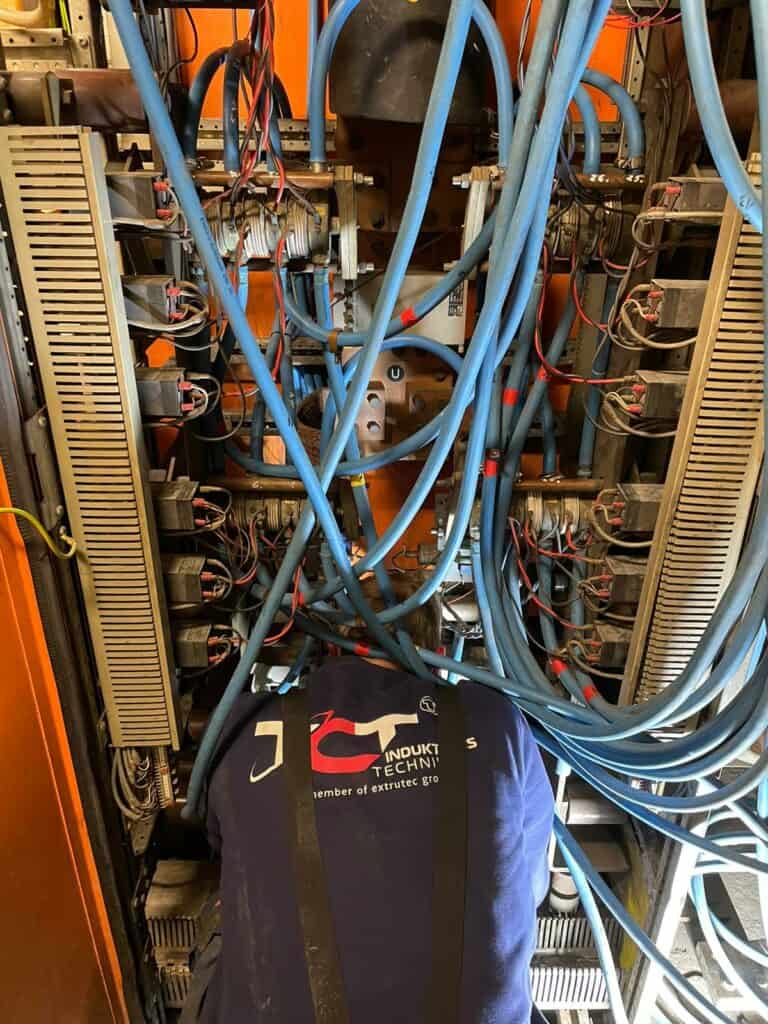
24/7 emergency service
Even when unexpected events happen, we are available as your service partner — networked worldwide and reachable at any time with immediate response times. If your induction systems experience a breakdown or faults, we’ll be on our way within 24 hours and, if necessary, on site over the weekend.
All repairs are carried out by our own specialists to the highest quality standards, and every task is fully documented in a detailed inspection report. When required, we also take care of removing and installing furnace linings or entire furnace assemblies right at your factory.
A large inventory of spare parts is immediately available, and we can also manufacture non-stock components in-house. Getting your production back up and running as fast as possible is our top priority.
In an emergency, contact us directly — our team is always available for you.
Training & assistance
An important part of the responsible handling of induction systems is the training and further education of the employees involved. We offer specific training in all areas from commissioning to daily operation and effective maintenance. Whether at our factory or at your site: In combination with our parent company, you benefit from the know-how we have built up together over the years in handling a wide variety of system types.
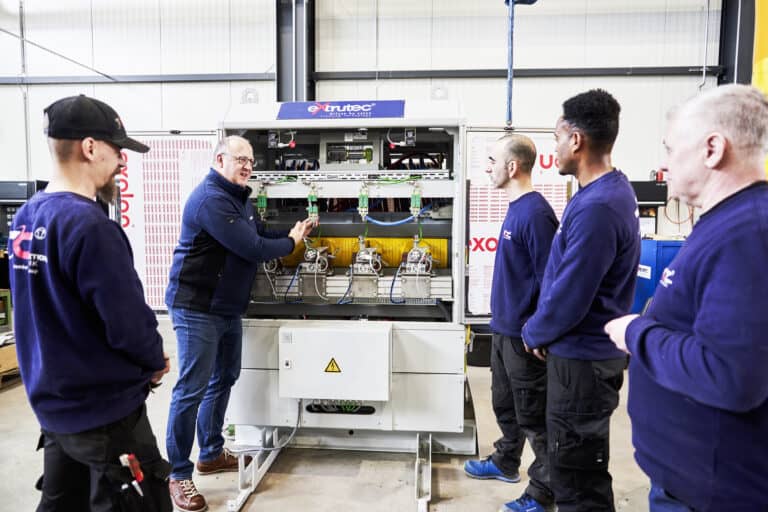
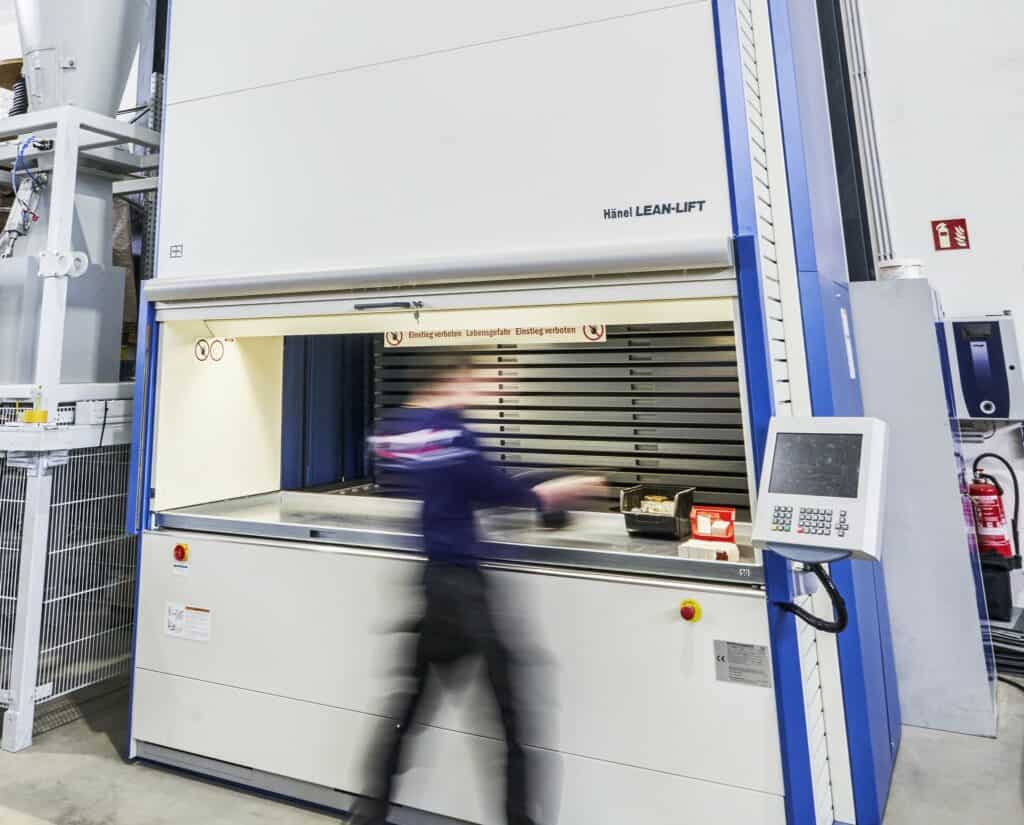
Storage and logistics
Our spacious production halls provide extensive storage capacity for the proper warehousing and logistics of a wide range of spare parts. This material availability enables us to optimize processes and ensure rapid response in emergencies, preventing downtime at our customers’ facilities. Equipped with the latest high-bay warehouse technology, we have direct access to your components at all times and can make them available for transportation on demand.
We are geared towards the high internal
and external customer requirements.
Complete systems and ovens can be set up and tested for pre-commissioning
on a production area of approx. 2,000 m².